Legosortiermaschine Sortierung
Teammitglieder: Tobias Brandt, Marc Eidhoff
Dies ist ein Unterartikel von der Legoteil_Zählmaschine, welcher den genauen Aufbau der Sortiereinheit beschreibt.
Die Sortiereinheit der Legosortiermaschine stellt einen der drei wichtigen Bereiche dar. Aufgabe der Sortiereinheit ist die Übernahme eines Legoteils von der Bildverarbeitung und der physikalische Transport in das richtige Fach.
Nach einer ausführlichen Ist-Analyse im letzten Semester wurde beschlossen, die Einheit von Grund auf neu zu konzipieren. Dafür wurde bereits ein umfangreiches CAD-Modell erstellt. Ziel in diesem Semester ist die Überprüfung und Umsetzung des Konzeptes. Außerdem wird die Servoansteuerung getestet und überarbeitet. Weitere Teilaufgaben des Teilteams Sortierung sind die Inbetriebnahme der gesamten Anlage, eine Gefährdungsbeurteilung sowie Komponententests neu erstellter Arduino Software.
Anforderungen und Ziele im Sommersemester 2018
Im Pflichtenheft wurden folgende Aufgaben festgehalten, welche im SS2018 bearbeitet werden sollen:
Spezifikations-ID | Anforderungs-ID | Anforderungstitel | Beschreibung der Spezifikation |
---|---|---|---|
020 | REQ10.2010 | Antriebe | Elektrischer Antrieb muss vorhanden sein |
030 | REQ10.2020 | Energieversorgung | Per 230V AC Schukostecker |
040 | REQ10.2030 | Abmessungen | 2,5m x 1m x 1,5m Grundplattenmontage |
051 | REQ10.2040 | Sicherheit/ Gefährdungsbeurteilung | Elektrische Sicherheit (Erdung metallischer Teile, Isolationskontrolle, Notabschaltfunktion) |
055 | REQ10.2040 | Sicherheit/ Gefährdungsbeurteilung | Gefährdungsbeurteilung: Welche Teile bringen welche Gefahr mit sich? |
056 | REQ10.2040 | Sicherheit/ Gefährdungsbeurteilung | Drucken und Anbringen von Warnhinweisen |
161 | REQ10.2320 | Sortierung der Legoteile in die Kästen | Kontaktaufnahme und Besprechung mit HSHL Hamm |
162 | REQ10.2320 | Sortierung der Legoteile in die Kästen | Kontrolle der SolidWorks Komponenten |
163 | REQ10.2320 | Sortierung der Legoteile in die Kästen | Umwandeln der ".sldprt" Dateien in ".dxf" Format |
164 | REQ10.2320 | Sortierung der Legoteile in die Kästen | Anpassen der ".dxf" Dateien für den LaserCutter (via IncScape) |
165 | REQ10.2320 | Sortierung der Legoteile in die Kästen | Fertigung der Teile mit Hilfe von 3D Drucker und Laserschneidsystem (Hamm) |
166.2 | REQ10.2320 | Sortierung der Legoteile in die Kästen | LaserCutter Teile kontrollieren und gegebenenfalls entgraten |
166.3 | REQ10.2320 | Sortierung der Legoteile in die Kästen | Wellen an die Klappen kleben |
166.7 | REQ10.2320 | Sortierung der Legoteile in die Kästen | PWM-Signal prüfen |
166.8 | REQ10.2320 | Sortierung der Legoteile in die Kästen | Funktionalität der Servomotoren herstellen |
166.9 | REQ10.2320 | Sortierung der Legoteile in die Kästen | Steckverbindung von Sortiereinheit und Schaltschrank |
170 | REQ10.2321 | Beschriftung für die Sortierung der Legoteile in die Kästen | Fächer mit Aufklebern des Inhalts markieren |
500.4 | REQ10.2380 | Komponententests | Für die Entwickelte Software bzw. Steuer- und Regelungsalgorithmen müssen geeignete Komponententests durchgeführt und geeignet dokumentiert werden |
Konstruktionsplanung
Zum besseren Verständnis werden die Teilkonzepte der letzten Semester noch einmal aufgegriffen und im folgenden Abschnitt erläutert:
Teilkonzept: Stellerbefestigung
Die Servos werden über Schrauben mit einem gedruckten 3D-Bauteil verbunden, welches wiederum über das bereits erwähnte Stecksystem und einem Alleskleber mit den Towern verbunden wird. (siehe 'Abb. 2')
Teilkonzept: Drehmomentübertragung
Sowohl an den Wellen, als auch an den Servos sind Flügelhörner angebracht.
Um eine Torsion zwischen Flügelhorn und Welle zu verhindern, muss das Ende der Welle so gebogen werden, dass diese in das zweite Loch gesteckt werden kann, bevor beides miteinander verklebt wird.
Zwischen beiden Flügelhörnern werden jeweils auf der linken und rechten Seite der Flügelhörner Federn gespannt, sodass die Klappen mit Druck an die Anschlagplatten gedrückt werden kann und eventuelle Steuerfehler (Zittern) minimiert werden. (siehe 'Abb. 3')
Teilkonzept: Vorsortierung
Die Vorsortierung in die drei Hauptkategorien „erkanntes Teil“, „erkanntes Fremdteil“ und „nicht erkanntes Teil“, wurde mit Hilfe von drei Klappen realisiert. (vgl. 'Abb. 4')
- Ist das Teil ein „erkanntes Fremdteil“, so fällt es einfach nach unten durch und alle Klappen sind in ihrer Extremposition an der Wand.
- Ist das Teil ein „nicht erkanntes Teil“, so befinden sich die beiden oberen Klappen in ihrer Extremposition an der Wand und die darunter liegende Klappe wird so gestellt, dass das Teil abgelenkt wird und in den Rückführschacht gelangt.
- Für die Kategorie „erkanntes Teil“ sind die beiden oberen Klappen zuständig. Soll das Teil in die weiße Einlage einsortiert werden, so stellt sich die rechte Klappe, bei der roten Einlage die Linke.
Teilkonzept: Rückführung
Derzeit ist für die Rückführung (siehe 'Abb. 4' & 'Abb. 5') eine Box geplant, die unter der Öffnung des Rückführschachts platziert wird.
Jedoch wäre auch ein Förderband möglich, welches nicht erkannte Teile wieder zurück in den Bunker befördert.
Dieses Förderband müsste dem entsprechend unter einem Winkel angebracht werden, um den Höhenunterschied von Öffnung Rückführschacht und Öffnung Bunker zu überbrücken.
Teilkonzept: Abbremsung
Für die Abbremsung wurde kein Fliegengitter, wie anfangs geplant, sondern ein Metallgitter verwendet, da dieses bei häufiger Nutzung oder Beschuss keine bis keine Verschleißerscheinungen aufweisen wird, anders wie beim Fliegengitter zu erwarten wäre.
Der Rahmen wurde bereits gedruckt und das Gitter mit diesem verklebt. (vgl. 'Abb. 6', Konstruktionsbild)
Teilkonzept: Betriebssicherheit
Die komplette Konstruktion der Sortiereinheit ist ein abgeschlossenes System, in welches sich während des Betriebs nur bedingt eingreifen lässt.
Die Deckel der Tower, sowie des Transportschachts von der Bildverarbeitungsbox zur Vorsortierung, sind mit einem kleinen Überstand versehen, sodass sie sich abnehmen ließen, sofern ein Eingreifen notwendig wäre.
Weiterhin sind alle Servos nach Möglichkeit auf der Rückseite oder an den Seiten, nicht aber auf der Vorderseite angebracht, sodass man dort nur schwierig mit den Fingern herein geraten könnte.
Ebenso sind die beiden Tower mit einem Verpolschutz auf der Grundplatte versehen, sodass sich die Einlagen der Legokästen weder falsch herum, noch vertauscht einsetzen lassen.
Anfertigung der Sortiereinheit
Die Sortiereinheit besteht aus 3D-Durck Teilen und Acrylglasplatten. Diese sind als CAD-Modelle in SVN abgelegt und müssen vorerst überprüft werden.
Prüfen des Konzepts
Bevor die Einzelteile der Sortieranlage gefertigt werden konnten musste das Gesamtkonzept und die Maßgenauigkeit geprüft werden. Dazu wurde eine Überprüfung jeder einzelnen Komponente im CAD-Modell vorgenommen es wurden die Maße, Passstellen, Verbindungsstücke und Materialstärken kontrolliert.
Ebenfalls wurde die Baugruppe zur Hilfe genommen und damit konnten mögliche Kollisionen ausgeschlossen werden. Das größte zu sortierende Legoteil passt demnach durch alle Schächte und wird an keiner Stelle eingeklemmt. Aus diesem Grund werden die CAD-Modelle ab diesem Zeitpunkt als in Ordnung angenommen und die weiteren Schritte eingeleitet.
Acrylglasplatten
Aufgrund des beschränkten Fertigungsraumes, sowohl des 3D-Druckers als auch des Lasercutters, mussten große Bauteile teils mehrfach getrennt und in sich steckbar sowie stabil, umkonstruiert werden. Alle 37 Bauteile, die aus Acrylglas gefertigt werden sollen, wurden bereits in SolidWorks so angeordnet, dass möglichst wenig Platten zur Herstellung aller Bauteile von Nöten sind. (vgl. 'Abb. 7')
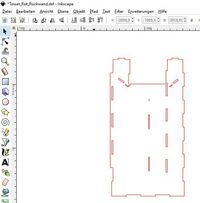
Absprache mit LaserCutter Hamm
Die Fertigung der Acrylglasplatten übernimmt das Prototyping Labor mit einem LaserCutter der Hochschule Hamm-Lippstadt am Standort Hamm. Dazu wurde ein Kontakt mit den zuständigen Betreuer hergestellt und es wurden weitere Informationen zu dem LaserCutter eingeholt. Hierbei wurde in der Stücklistefestgestellt, dass Teile zu groß waren. Nach einer genaueren Kontrolle der CAD-Modelle stellte sich jedoch heraus, dass hier die Maße der zusammengestzen Baugruppen und nicht die der einzelnen Teile eingetragen wurden. Diese Fehler wurden behoben.
Eine weitere Forderung war zudem ein spezielles Dateiformat der CAD-Modelle für den LaserCutter. Die CAD-Modelle wurden von dem ".SLDPRT"-Format in Vektorgrafiken(.dxf) umgewandelt, damit diese an die zuständigen wissenschaftlichen Mitarbeiter (Ansprechpartnerin Herr Björn Schmidt) in Hamm für den Lasercutter geschickt werden konnten.
Diese Umwandlung der SolidWorks Dateien stellte das Programm leider nicht zur Verfügung, weshalb das kostenfrei nutzbare Programm Inkscape zu Hilfe geholt werden musste.
Hierzu wurden die SolidWorks Dateien importiert, Schneidelinien rot(ff0000) und 0,01 mm stark sein, sowie die sämtliche Beschriftungen entfernt. Anschließend wurde die Datei im bereits genannten '.dxf'-Format gespeichert. Damit die Übersicht nicht verloren ging, welche Dateien schon umgewandelt wurden, musste in der Stückliste in der alle Bauteile eingetragen sind eine Spalte ergänzt werden in der abgehakt wurde welche Dateien schon vorhanden sind.
In Abbildung 8 ist eine Bearbeitung eines Teiles mit der Software InkScape zu sehen:
Die IncScape Dateien wurden in SVN abgelegt: IncSkape-Dateien.
Bestellen der Materialien
Eine Anforderung des Labors ist eine maximale Materialgröße von 300mm x 600mm. Daraufhin wurde die Stückliste, in welcher alle Teile mit ihren Maßen beschrieben sind, überprüft. Anschließend wurde die Stückliste auf Anzahl der Lasercutterteile in Hinblick auf der benötigten Stärke durchgeschaut.
Es werden 19 Platten â 3mm Stärke und 30 Platten â 5mm Platten benötigt. Mit diesen Informationen wurde eine Vielzahl von Angeboten verglichen und der günstigste Anbieter ausgewählt. Die Bill of Material wurde an Prof. Dr. Göbel weitegeiletet, sodass die Materialien bestellt wurden. Die Lieferung erfolgte direkt an das Prototyping Labor in Hamm.
Die Bestelliste ist in SVN abgelegt: BOM Plexiglas
Musterfertigung
Es ist wichtig, dass der Laser genau arbeitet und die Schnittlinien eingehalten werden. Die Steckverbindungen dürfen nicht zu locker und nicht zu fest sitzen. Aus diesem Grund wurden nicht direkt alle LaserCutter Teile in Auftrag gegeben, sondern erst einmal nur zwei Teile. Mit diesen wurde ein Probeaufbau realisiert indem die beiden Platten (eine Außenwand des Towers) zusammengesteckt wurden. In Abbildung 9 ist zu erkennen, dass Teil A und Teil B die Passbedingungen erfüllen und wie ein Puzzle zusammengesetzt werden können.
Auffällig hierbei war es, dass ein geringes Spiel vorhanden ist und die deshalb Teile vorraussichtlich, wie geplant, zusätzlich verklebt werden müssen. Dafür ist eine Nacharbeit (z.B. Entgraten) nicht erforderlich.
Aufgrund der Passgenauigkeit wurden die restlichen Teile bei dem Prototyping Labor in Hamm bestellt.
3D-Druckteile
Prüfen und übergeben
Bei dem Prüfen des Konzeptes wurden bereits die CAD-Modelle kontrolliert. Für die Sortiereinheit werden 93 zu druckende 3D-Druckteile benötigt. Diese wurden mit der Stückliste zusammen an den wissenschaftlichen Mitarbeiter Ilya Raza übergeben. Auch hier wurden Probeteile gefertigt, damit ein Testaufbau mit den Acrylglasplatten realisiert werden konnte. Dafür wurden eine Klappe und zwei seitliche Anschläge abgeholt und weiterverarbeitet. Aufgrund des 3D-Drucks sind die gedruckten Teile nachzuarbeiten. Wie in Abbildung 10 zu erkennen, muss das Stützmaterial aus den Hohlräumen sowie die Rafts entfernt werden. Desweiteren ist eine Entgratung notwendig.
Testaufbau
Nachdem nun Probeteile der Acrylglasplatten und 3D-Teile gerfertigt und nachbearbeitet wurden, wird ein Testaufbau eines Teiles der Sortiereinheit realisiert. Eine Klappe besteht dabei aus zwei zusammengesetzten 3D-Druckteilen. Die Steckverbinding dieser Teile erwies sich als schwierig. Eine sehr genaue und zeitintensive Nacharbeit der 3D-Druckteile ist deshalb erforderlich.
Der gesamte Testaufbau besteht aus einer Verbindung einer Klappe mit zwei Anschlägen (3D-Druckteile) mit einer zusammengesteckten Außenwand (Acrylglas). In Abbildung 11 ist dieser Testaufbau zu sehen.
Ergebnisse aus dem Testaufbau sind:
- sehr genaue Nachbearbeitung der 3D-Druckteile erforderlich
- kleben der segmentierten 3D-Druckteile und Acrylglasplatten notwendig
- keine Nachbearbeitung der Acrylglasplatten nötig
- Steckverbindungen sind passgenau
Die restlichen 3D-Druckteile befinden sich in der Fertigung und werden voraussichltich im September 2018 zur Verfügung stehen.
Servomotoren
Die Servomotoren sind für die Bewegung der Klappen vorgesehen. Im der gesamten Sortiereinheit werden 11 Servomotoren verwendet. Angesteuert werden diese über die PWM-Anschlüsse des Arduinos und einer Steuerleitung. Die Servos müssen nach einem vorher definierten Winkel verstellt werden können. Als Endergebnis soll die automatische Sortierung der Legoteile in die Sortierkisten über die Klappen erfolgen. Aufgrund von Zeitmangel aus dem letzten Semester konnten die Motoren allerdings nicht richtig angesteuert werden. Dieses zeigte sich durch "zucken" oder Stillstand einiger Motoren.
Ausgangszustand:
- 10 Meter Signalkabel
- "Lötkugel" für die Spannungsversorgung
- Lötverbindungen an den Steckern können sich leicht berühren (Kurzschlussgefahr)
Aufbau einer Testplatine
Um Störeinflüsse der Leitungen zu den Servomotoren zu untersuchen wurde eine Platine, wie in Abbildung 12 zu sehen, mit passenden Steckern angefertigt und direkt über ca. 30cm lange Leitungen an den Arduino angeschlossen. Durch die Platine können sich die einzelnen Steckerkontakte nicht mehr berühren. Die Steckverbindungen zu den Servos können so erleichtert verwendet werden ohne Kurzschlüsse zu verursachen. Seitlich von den Steckkontakten sind auf der Platine die Signalleitungen herausgeführt, die an die Steuerelektronik verbunden werden können.
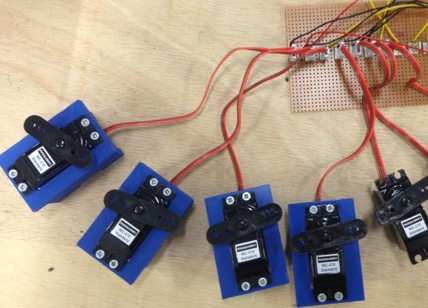
Um das 10m Signalkabel als Fehlerquelle auszuschließen wurde die Testplatine direkt an den Arduino im Schaltschrank angeschlossen. Nach dem Erstellen und anschließen der Platine an den Arduino wurde das PWM-Signal am Ausgangspin direkt gemessen und mit dem Signal an der Platine verglichen. Da das Signal an beiden Messstellen identisch war und einen ausgeprägten Rechteckimpuls darstellte ist der Grund für die Störungen und des nicht Funktionierens in der Programmierung zu suchen.
Ansteuerung der Servos
Eine Recherche hat ergeben, dass der Befehl Servo.write eine falsche Pulsweite ausgibt. Diese Pulsweite kann über die Bibliothek Servo.h verändert werden. Die Winkelstellung der Servos erfolgt anschließend über eine Pulslänge.
Einige Servos (z.B. wie das verwendete Modell „MC-410“) benötigen zur Ansteuerung eine andere Pulslänge als die Standardeinstellung in Arduino. Im folgendem Beispielprogramm (Abbildung 13) ist der Test eines Servos mit angepasster Pulsweitenbreite implementiert worden. Dieses Programm dient zum Test eines einzigen Servomotoren und ist unter folgendem Link zu finden: Servotest
Die Erklärung wie die Pulsweite angepasst werden kann ist unter folgendem Link zu finden: Pulsweitenanpassung
Unter Verwendung der Pulsweitenänderung wurde das PWM- Signal mit Hilfe eines Oszilloskops wie in folgender Abbildung zu erkennen überprüft. Hier ist zu erkennen, dass beide Kanäle (in diesem Fall Servomotor 1 und 2) über einen eindeutigen Rechteckimpuls angesteuert werden. Somit ist die Ansteuerung fehlerfrei und funktionsfähig.
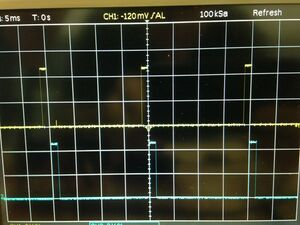
Hiernach musste der Rückbau stattfinden, sodass die Servosmotoren nicht mehr direkt im Schaltschrank angeschlossen sind, sondern an der Position der späteren Sortiereinheit Verwendung finden können.
Dafür wurde das 10m lange Signal und das 10m lange Spannungsversorgungskabel auf ca.3m gekürzt.
Da die Platine nur zu Testzwecken diente und ein beliebiges Vertauschen der Motoren möglich ist wurde am Ende des Signalkabels ein Sub-D Stecker anglötet. Hierdurch wird eine fester Anschluss der Motoren gewährleistet. In Abbildung 15 ist der Stecker zu sehen. Auf der rechten Seite ist das Signal- und Spannungsversorgungskabel zu erkennen. Auf der linken Seite führen die Steuerleitung zu den Servos (hier noch auf die Testplatine), da die Leitungslängen zu den Servos noch nicht feststehen.
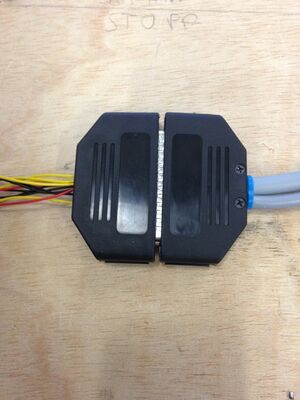
Abschließend wurde ein Funktionstest der einzelnen Motoren durchgeführt. Dabei stellte sich heraus, dass 4 von den 11 Motoren nicht funktionstüchtig waren und somit nachbestellt werden mussten.
Das Vorgehen der Prüfung und der Fehlerbehebung wurde in einem Komponententest festgehalten und ist unter folgendem Link zu finden:
Einsortierung
Fächer mit Aufklebern des Inhalts markieren
Für die Einsortierung der Legoteile in die entsprechenden Kisten wurden diese mit Aufklebern versehen (siehe Abbildung 38).
-
Abb. 38: Aufkleber in den Fächern der Kiste
-
Abb. 39: Liste der Legoteile
Außerdem wurde eine Liste erstellt, welche die Anzahl der Teile beinhaltet. Die Liste wurde ausgedruckt und zur Sortiermaschine gelegt und zedem an folgendem Speicherort abgelegt:
Quelle: SVN_SDE_LegoSortiermaschine\Teams\Sortierung\Einsortierung\Einsortierung.xlsx
Ausblick/Finaler Stand
In den beiden Semestern SS17 und WS17/18 wurden verschiedene Sortierverfahren validiert, verifiziert und evaluiert.
Bei der Gegenüberstellung der verschiedenen Sortierverfahren, ergab sich als beste Lösung eine Klappenbox mit der Möglichkeit, in die originalen Einlagen der Legokisten zu sortieren.
Alle Einzelheiten der Klappenbox wurden in Teilkonzepten vorentworfen und anschließend in CAD umgesetzt.
Weiterhin wurden schon die ersten Schritte zur Fertigung und Inbetriebnahme gesetzt, indem die Arduinosoftware zur Ansteuerung der Servos erweitert wurde (Link), sowie schon einige 3D-Druckteile bereits gefertig wurden (Link).
Eine Übersicht über sämtliche Bauteile befindet sich im SVN.
Im kommenden Sommersemester 18 sind noch folgenden Aufgaben zu erledigen, um das Projekt erfolgreich abzuschließen:
- Umwandlung der ".SLDPRT"-Dateien in ".svg"-Dateien via Inkscape
- Fertigung der Platten
- Fertigung der 3D-Druckteile
- Zusammenbau
- Inbetriebnahme
Dies ist ein Unterartikel von der Legoteil_Zählmaschine, welcher den genauen Aufbau der Sortiereinheit beschreibt.