Legosortiermaschine Separierung: Unterschied zwischen den Versionen
(239 dazwischenliegende Versionen von 6 Benutzern werden nicht angezeigt) | |||
Zeile 1: | Zeile 1: | ||
Teammitglieder: [[Benutzer:Madlen Bartnick|Madlen Bartnick]], [[Benutzer:Jerome Wolf|Jerome Wolf]], | |||
<br /> | <br /> | ||
[[Datei:VorderseiteLegoteilzählmaschine1819.jpg|500px|thumb|rechts|Abb. 1: Vorderseite der Legoteil Zählmaschine]] | |||
Dies ist ein Unterartikel von der [http://193.175.248.52/wiki/index.php/Legoteil_Z%C3%A4hlmaschine Legoteil_Zählmaschine], welcher den genauen Aufbau der Separierung beschreibt. | |||
[[Datei:RueckseiteLegoteilzählmaschine1819.jpg|500px|thumb|rechts|Abb. 2: Rückseite der Legoteil Zählmaschine]] | |||
<br /> | <br /> | ||
Die Separierung ist die erste Teilaufgabe der Legosortiermaschine. Sie sorgt dafür, dass die Legoteile einzeln und zentriert in die Bildverarbeitungsbox fallen, da dort nur einzelne Teile erkannt werden können. | |||
<br /> | <br /> | ||
<br /> | <br /> | ||
Der aktuelle Aufbau der Separierung besteht aus einem Steigförderband mit Bunker (Abb. 1 Pos. 1). Dort werden die zu sortierenden Legoteile dem System zugeführt. Das Steigförderband transportiert eine Teilmenge der zugeführten Legoteile in eine darunterlegende Vibrationsförderrinne (Abb. 2 Pos. 2), in der diese dann zentriert und weiter vereinzelt werden. Durch die Vibration gelangen die Teile auf ein weiteres Förderband, welches diese durch eine Separierungsbox (Position 3) transportiert. | |||
Die in der Separierungsbox integrierte Kamera liefert Momentaufnahmen der auf dem Transportband beförderten Teile. Mittels Bildverarbeitung wird die Anzahl der auf dem Band liegenden Teile in einem festgelegten Bereich ermittelt. Falls sich mehrere Teile in diesem Bereich befinden, werden mit Hilfe von Druckluftdüsen gezielt einzelne Teile in einen Auffangbehälter befördert. Nach der Separierungsbox befinden sich die Teile einzeln und zentriert auf dem Förderband und fallen von dort aus zur Erkennung in die Bildverarbeitungsbox (Abb. 1 Pos. 4). | |||
Durch diesen Aufbau wurde das im Sommersemester 18 entwickelte Konzept zur Verbesserung der Separierung umgesetzt. | |||
<br /> | <br /> | ||
Ansatzpunkte des Konzepts: | |||
* Modifikation des Steigförderbands zur besseren Vereinzelung der Teile | |||
* Integration einer Vibrationsförderrinne zur Zentrierung der Teile | |||
* Umbau der Separierungsbox zur Aussortierung nicht vereinzelter Teile | |||
<br /> | <br /> | ||
Die Umsetzung des Konzepts im Wintersemester 18/19 soll Inhalt dieses Artikels sein. | |||
<br /> | <br /> | ||
<ref name="Autor: Bartnick"> Autor Madlen Bartnick</ref> | |||
=Modifikation des Steigförderbands zur besseren Vereinzelung der Teile= | |||
Da das Steigförderband im Ausgangszustand viel zu viele Teile auf einmal befördert hat (vgl. Abb. 5), wurde dieses modifiziert. Dazu wurden im vorherigen Semester ein neuer Fördergurt und Stollenmaterial bestellt, welche in diesem Semester dann durch Klebeverbindungen zu einem individuellen Stollengurt zusammengefügt wurden. Dabei wurden die Stollen zunächst provisorisch befestigt und verschiedene Anordnungen getestet. Nach und nach wurden die Stollen entfernt und verkleinert, bis sich das optimale Layout für die Vereinzelung ergeben hat (vgl. Abb. 6). In diesem Layout sind nun über den gesamten Gurtumfang verteilt sechs Stollen angebracht, die gemeinsam die gesamte Breite des Gurtes einmal abdecken. Damit die Teile neben den kleinen Stollen nicht aus dem Bunker fallen, musste der Abstreifer angepasst werden. Dazu wurde dieser in schmale Streifen geschnitten, sodass er sich automatisch an die Größe der Stollen anpassen kann. Um die Gesamtstabilität zu erhalten, wurde ein Blech angefertigt und zusammen mit dem Abstreifer oberhalb der Stollen eingebaut (vgl. Abb. 7). Das Ergebnis der Modifikation ist nun eine wesentlich geringere Menge an Teilen, die gleichzeitig durch das Steigförderband gefördert werden (vgl. Abb. 8). | |||
<gallery widths="300" heights="450"> | |||
Datei:Bunkerband_alt.jpg|Abb. 5: Steigförderband vor der Modifikation | |||
Datei:BandNeu.jpg| Abb. 6: Neues Layout der Stollen | |||
Datei:BandBeispielstollenl.jpg|Abb. 7: Abstreifer zwischen Bunker und Stollen | |||
Datei:Bunkerband_mod.jpg|Abb. 8: Steigförderband nach der Modifikation | |||
</gallery> | |||
<ref name="Autor: Bartnick"> Autor Madlen Bartnick</ref> | |||
=Integration einer Vibrationsförderrinne zur Zentrierung der Teile= | |||
Um die Teile, die von dem Steigförderband aus dem Bunker befördert werden weiter zu vereinzeln und zusätzlich zu zentrieren, wurde eine Vibrationsförderrinne in den Prozess integriert. Zuvor sind die Teile vom Steigförderband aus dem Bunker direkt auf das Förderband gefallen, welches durch die Separierungsbox zur Bildverarbeitungsbox führt. Dabei wurden die Teile nicht gleichmäßig sondern haufenweise auf dem Förderband verteilt. Diese Haufen führen im weiteren Prozess zu Problemen, da die Bildverarbeitung nur einzelne Teile erkennen kann. Durch die Integration der Vibrationsförderrinne wurde die Haufenbildung auf dem Förderband erheblich gesenkt, da diese die Teile weitgehend hintereinander und zentriert auf das Förderband legt. | |||
Die zur Integration durchgeführten Arbeitsschritte werden nachfolgend genauer erläutert. | |||
===Montage des Vibrationsantriebs in der Anlage=== | |||
Um die Vibrationsförderrinne in den Prozess integrieren zu können, musste im ersten Schritt das Förderband, welches durch die Separierungsbox führt, durch ein kürzeres Förderband ersetzt werden. Danach wurde eine Grundplatte aus Aluminiumprofil und Holz erstellt (vgl. Abb. 9). Auf diese Grundplatte wurde im nächsten Schritt der Vibrationsantrieb montiert (vgl. Abb. 10). Zum Schluss wurde die Grundplatte mit Vibrationsantrieb durch zwei höhenverstellbare Ständer unterhalb des Bunkerbandes montiert (vgl. Abb. 11). | |||
<gallery widths="425" heights="250"> | |||
Datei:Grundplatte.png|Abb. 9: Aufbau der Grundplatte | |||
Datei:GrundpatteMitVibrorinne.png|Abb. 10: Vibrationsantrieb montiert auf der Grundplatte | |||
Datei:VibrorinneEingebaut.png|Abb. 11: Montage innerhalb der Anlage | |||
</gallery> | |||
===Elektrischer Anschluss und Ansteuerung des Vibrationsantriebs=== | |||
Nachdem der Vibrationsantrieb mechanisch integriert wurde, musste dieser elektrisch eingebunden werden. Dazu wurde er zunächst wie in vorherigen Semester geplant angeschlossen. Der erste Test zeigte jedoch, dass die Vibrationsleistung sowie die dadurch verursacht Lautstärke viel zu groß war. Daraufhin wurde durch einen [http://svn.hshl.de/svn/MTR_SDE_Praktikum_2015/trunk/Dokumentation/02_Versuchsprotokolle/Optimierung%20Vibrationsf%C3%B6rderrinne/Versuchsprotokoll_Optimierung_Vibrationsf%C3%B6rderrrinne.docx Versuch] die optimale Spannung zur Ansteuerung des Vibrationsantriebs ermittelt und ein Widerstand vorgeschaltet (vgl. Abb. 12). Dadurch wurden Leistung und Geräuschentwicklung optimiert und die Vibrationsförderrinne konnte auch programmtechnisch ins System integriert werden. Dazu wird diese gemeinsam mit dem Förderband, welches durch die Separierungsbox führt, gestartet und gestoppt (vgl. Abb. 13). | |||
<gallery widths="660" heights="500"> | |||
Datei:AnschlussVibrationsantrieb.png|Abb. 12: Verdrahtungsschema des Vibrationsantriebs | |||
Datei:AnsteuerungVibrationsantrieb.jpg|Abb. 13: Ansteuerung des Vibrationsantriebs über den Arduino | |||
</gallery> | |||
===Konstruktion der Förderrinne=== | |||
Nach der Integration des Vibrationsantriebs in den Prozess folgte die Konstruktion der Förderrinne, in der die Teile später von dem Abwurf des Bunkerbands bis zum nachfolgenden Förderband transportiert werden. Dazu wurde im vorherigen Semester eine Rinne mit halbrundem Profil als beste Fördermöglichkeit ermittelt. Damit diese Förderrinne auf dem Vibrationsantrieb montiert werden kann, ohne dass die Schraubverbindungen im Inneren der Förderrinne liegen, wurde eine Montageplatte als Verbindungsglied konstruiert (vgl. Abb. 14). Diese Montageplatte soll auf den Vibrationsantrieb mittels Zylinderkopfschrauben befestigt werden. Die Förderrinne soll über eine trapezförmige Führungsschiene eingeschoben und mit einem Endstück mit vier Schrauben in der Führung fixiert werden. Die Förderrinne wurde so lang konstruiert, dass sie sich mit dem Förderband knapp überschneidet. Dadurch ist eine einwandfreie Übergabe gewährleistet. Das halbrunde Profil wurde so ausgelegt, dass auch das breiteste Legoteil problemlos gefördert werden kann. Die Unterseite der Förderrinne wurde mit dem Gegenstück der trapezförmigen Führungsschiene versehen (vgl. Abb. 15). So können die Einzelteile zusammen mit dem Vibrationsantrieb zum Gesamtsystem Vibrationsförderrinne zusammengesetzt werden (vgl. Abb. 16). | |||
Die erstellten [http://svn.hshl.de/svn/MTR_SDE_Praktikum_2015/trunk/Teams/Separierung/Konstruktion%20Vibrationsf%C3%B6rderrinne CAD-Dateien] sind in SVN hinterlegt. | |||
<gallery widths="425" heights="250"> | |||
Datei:Montageplatte.png|Abb. 14: Montageplatte zur Verbindung von Vibrationsantrieb und Förderrinne | |||
Datei:Förderrinne.png|Abb. 15: Förderrinne | |||
Datei:Gesamt.png|Abb. 16: Gesamtansicht der Vibrationsförderrinne | |||
</gallery> | |||
===Druck und Einbau der Förderrinne=== | |||
Nach Abschluss der Konstruktion wurden die Teile mit Hilfe eines 3D-Druckers hergestellt (vgl. Abb. 17). Im Anschluss daran wurden diese Teile nachbearbeitet und auf dem Vibrationsantrieb montiert (vgl. Abb. 18). Nach der Optimierung des Zusammenspiels zwischen den Förderbändern und der Vibrationsförderrinne wurde der Übergang von dem Steigförderband zur Vibrationsförderrinne durch Zusammensetzen mehrerer durch 3D-Druck hergestellter Teile und einer Plexiglasscheibe so gestaltet, dass alle Teile sicher in die Förderrinne fallen (vgl. Abb.19). | |||
<gallery widths="425" heights="250"> | |||
Datei:DruckFörderrinne.png|Abb. 17: Druck der Förderrinne | |||
Datei:EinbauFörderrinne.png|Abb.18: Montage der Förderrinne | |||
Datei:ÜbergangBunkerband.png|Abb. 19: Übergang zwischen Bunkerband und Vibrationsförderrinne | |||
</gallery> | |||
<ref name="Autor: Bartnick"> Autor Madlen Bartnick</ref> | |||
= Überarbeitung der Separierungsbox = | |||
Da bei der ehemaligen Box zur finalen Vereinzelung die Teile auf dem Band zurückgeschoben wurden, würde dieses Vorgehen das komplette Konzept der Vereinzelung und Zentrierung durch das modifizierte Band und die Vibrationsförderrinne stören, da sich auf diese Weise erneut die unerwünschten Teilehaufen bilden würden. Durch die nach aktuellem Stand voraussichtlich sehr gut Vereinzelung vor der Bildverarbeitungsbox, wurde diese so umgebaut, dass Teile, welche zu nahe beisammen liegen, aus dem System befördert werden. Diese können im späteren Verlauf der Teilerückführung zugeführt werden und werden so erneut verarbeitet. Ein Stillstand durch die Bildung von Teilehaufen wie beim alten Konzept wird so vermieden. | |||
== Umbauarbeiten == | |||
Um das neue Konzept umzusetzen mussten zunächst einige Umbauarbeiten vorgenommen werden. | |||
=== Umbau des Förderbandes === | |||
Um Platz für die [[#Integration einer Vibrationsförderrinne zur Zentrierung der Teile | Integration einer Vibrationsförderrinne zur Zentrierung der Teile]] zu schaffen, musste vor dem Umbau der Separierungsbox jedoch zunächst das darunter liegende Förderband verkürzt werden. Hierzu wurde das von vohrerigen Iterationen der Maschine übrig gebliebene Band verwendet, da dieses bereits die idealen Abmaße besaß. Somit wurde das alte Band demontierung und ohne großen Aufwand durch das alternative Band ersetzt. Zudem wurden Bandbegrenzung und Halterung für die Box modifiziert, um einen seitlichen Auswurf der Teile zu erlauben. Der Gesamte Bandaufbau vor der Montage der Separierungsbox ist in Abb. 20 zu sehen. | |||
<gallery widths="400" heights="200"> | |||
Datei:Foerderband_Umbau_Auswurf.jpg | Abb. 20: Umgebautes Förderband mit Lücke für Teileauswurf | |||
</gallery> | |||
=== Konstruktion und Aufbau der neuen Bildverarbeitungsbox === | |||
Die neue Separierungsbox wurde zunächst in CAD Konstruiert, wie in Abb. 21 und Abb. 22 zu sehen. Das Design lehnt sich dabei an die alte Separierungsbox an, wobei entsprechende Änderungen wie seitliche Schlitze für die Düsen, sowie eine große Lücke für den Auswurf eingearbeitet wurden. | |||
<gallery widths="450" heights="250"> | |||
Datei:Separierungsbox_Auswurf_CAD_1.png | Abb. 21: CAD Modell Ansicht 1 | |||
Datei:Separierungsbox_Auswurf_CAD_2.png | Abb. 22: CAD Modell Ansicht 2 | |||
</gallery> | |||
Anschließend wurde die Box aus Holz gefertigt. Dazu wurden zunächst die einzelnen Holzplatten zusammengeschraubt, sowie die entsprechenden Ausschnitte und Löcher hinzugefügt. Nach der Montage von LEDs (Abb. 24) und Düsen (Abb. 23) wurde die Box auf dem Förderband Montiert. Diese erste Version der neuen Box ist in Abb. 25 zu sehen. | |||
<gallery widths="450" heights="250"> | |||
Datei:Separierungsbox_Duesenanbringung.jpg | Abb. 23: Anbringung der Druckluftdüsen | |||
Datei:Separierungsbox_Auswurf_LEDs.jpg | Abb. 24: LED-Konfiguration in der Box | |||
Datei:Separierungsbox_Auswurf_1.jpg | Abb. 25: Erste Version der neuen Box | |||
</gallery> | |||
Im weiteren Verlauf wurden noch einige kleine Änderungen vorgenommen. So waren die Düsen in den alten Halterungen nicht frei Drehbar, was für eine sehr eingeschränkte Flexibilität bei Montage und Positionierung sorgte. Entsprechend wurden auch neue Düsenhalterungen in CAD konstruiert und 3D-gedruckt. Dadurch können die Düsen nun frei gedreht werden und sind in der Positionierung flexibler. Insbesondere konnten die Düsen somit näher zusammengebracht werden, wodurch der Separierungsalgorithmus die Teile besser aus dem System befördern kann. | |||
<gallery widths="450" heights="250"> | |||
Datei:Duesenhalter_CAD.png | Abb. 26: CAD Modell der neuen Düsenhalter | |||
Datei:Separierungsbox_Auswurf_2.png | Abb. 27: Finale Version der neuen Box mit neuen Düsenhaltern und verbesserter Düsenposition | |||
</gallery> | |||
== Separierungsalgorithmus == | |||
[[Datei:Programmablauf_Separierung_Auswurf.png | 200px | thumb | rechts | Abb. 28: Ablaufplan des Separierungsalgorithmus ]] | |||
Nach den Umbauarbeiten an der Box wurde der entsprechende Steuerungsalgorithmus implementiert. | |||
=== Farbfilter === | |||
Die Erkennung von einzelnen Teilen in der Separierungsbox ist mithilfe einer Farbmaske realisiert. Dabei wird die Farbe des Förderbandes, welches sich unter den Teilen befindet, aus dem Bild herausgerechnet. Übrig bleiben entsprechend die einzelnen Teile auf dem Band. Zwar können auf diese Weise nicht alle Teile zu 100% einzeln erkannt werden, jedoch stellen die auf diese Weise nicht identifizierbaren Teileanhäufungen eine eher seltene Ausnahme dar. Die Farbmaske kann dabei mit dem sogenannten Color Thresholder in MATLAB erstellt werden. Der entsprechende Prozess ist bereits in der [[Legosortiermaschine_Bildverarbeitung#Farberkennung | Maskenbildung der Bildverarbeitung]] erklärt und kann dort entsprechend nachvollzogen werden. Das Ergebnis nach diversen Iterationen mit verschiedenen Masken und Kameraeinstellungen ist in Abb. 29 zu sehen. | |||
<gallery widths="500" heights="250"> | |||
Datei:Farbmaske_Separierung_Auswurf.png | Abb. 29: Farbmaske der Separierung | |||
Datei:Ansteuerungsbeispiel_Separierung_Auswurf.png | Abb. 30: Beispiel für Düsenansteuerung der Separierung | |||
</gallery> | |||
=== Programmablauf === | |||
Der Algorithmus der Separierung folgt anschließend im Grunde einem einfachen Ablauf: | |||
# Die benötigten Parameter für serielle Kommunikation, Bildbearbeitung und Separierung werden festgelegt. | |||
# Das Bild wird aufgenommen und der Farbfilter wird angewendet. | |||
# Die resultierende Binärmaske wird zugeschnitten um unerwünschte Bildbereiche zu entferne, kleine Objekte (Artefakte) werden gelöscht und die Schwerpunkte aller übrigen Objekte werden berechnet. | |||
# Sind die Schwerpunkte der Objekte in X-Richtung zu nahe beieinander und befindet sich das hintere Teil vor einer Düse, so wird dieses aus dem System befördert. | |||
# Zur Visualisierung werden das Originalbild und die Binärmaske mit Schwerpunkten, sowie die Düsen mit aktuellem Ventilzustand (blau = geschlossen, rot = geöffnet) in der GUI angezeigt. | |||
Der genaue Ablauf ist zudem nochmals graphisch in Abb. 28 dargestellt. In Abb. 30 ist hingegen eine beispielhafte Visualisierung der Ansteuerung zu sehen. Nach der Anwendung der Farbmaske und dem Zuschneiden des Bildes sind die einzelnen Teile in Weiß zu erkennen. Die Schwerpunkte der Teile werden durch einen kleinen roten Kreis dargestellt. Da sich im Konkreten Beispiel das Teil auf der linken Seite zu nahe am vorherigen Teil befindet und dieses sich zudem vor einer der beiden Düsen befindet, wird die Düse aktiviert und würde das Teil somit aus der Box befördern. | |||
<ref name="Autor: Wolf"> Autor Jerome Wolf</ref> | |||
= Teilerückführung = | |||
Die Teilerückführung soll dazu dienen, dem Bunker nicht erkannte sowie ausgeworfene Teile erneut zuzuführen. Dabei wurden verschiedene Optionen in Erwägung gezogen, welche im Folgenden genauer erläutert werden sollen. | |||
== Bewertung der Rückführungsoptionen == | |||
=== Prinzipielle Bewertung === | |||
Zunächst wurden für die Rückführung folgende grundsätzlichen Rückführungsmöglichkeiten in Erwägung gezogen: | |||
{| class="wikitable" | |||
|- | |||
! | |||
! Förderband | |||
! Schneckenförderer | |||
! Druckluftförderung | |||
! Teilerutsche | |||
|- | |||
! Vorteile | |||
| | |||
*Einfach | |||
*Erprobt | |||
| | |||
*Kompakt | |||
*Zuverlässig | |||
| | |||
*Günstig | |||
*Kompakt | |||
| | |||
*Sehr Günstig | |||
*Simpel | |||
|- | |||
! Nachteile | |||
| | |||
*Steigung Begrenzt | |||
*Teuer | |||
| | |||
*Teile können zerquetscht werden | |||
*Teuer | |||
| | |||
*Begrenzte Steigung und Teilegröße | |||
*Teile werden herum-geschleudert | |||
| | |||
*Teile können nur abwärts befördert werden | |||
|- | |||
! Umsetzbarkeit | |||
| Theoretisch machbar, Steigung ggf. problematisch | |||
| Zerquetschte Teile nicht akzeptabel | |||
| Nicht zuverlässig genug | |||
| Durch Höhenunterschied nicht machbar | |||
|} | |||
=== Typen von Steigförderbändern === | |||
Da die einfacheren oder experimentellen Methoden bei der Rückführung kein gutes Ergebnis versprachen, fiel die Auswahl letztendlich auf das erprobte Förderband zur Rückführung. Jedoch gibt es auch hier verschiedene Arten die in Frage kämen: | |||
{| class="wikitable" | |||
|- | |||
! | |||
! Steigförderband | |||
! Knickförderband | |||
! Z-Förderband | |||
|- | |||
! Vorteile | |||
| | |||
*Günstigste Alternative | |||
*Mechanisch einfach | |||
| | |||
*Gute Teileaufname durch gerade Strecke | |||
| | |||
*Gute Teileaufnahme | |||
*Viel Platz unter Teileabwurf | |||
|- | |||
! Nachteile | |||
| | |||
*Wenig Platz für Teileaufnahme | |||
*Wenig Platz unter Teileabwurf | |||
| | |||
*Wenig Platz für Teileabwurf | |||
*Durch gerade Aufnahme höhere Steigung | |||
| | |||
*Sehr hohe Steigung an Schräge durch gerade Aufnahme und Abwurf | |||
|- | |||
!Umsetzbarkeit | |||
|Nicht möglich da Teileaufnahme an Separierung nicht möglich | |||
|Möglich, aber Teileabwurf ungünstig | |||
|Ideal, aber Platz- und Steigungstechnisch schwierig | |||
|} | |||
== Anfragen bei Herstellern == | |||
[[Datei:Abmessungen_Rueckfuehrungsband.png | 500px | thumb | Abb. 31: Abmessungen möglicher Rückführungsbänder ]] | |||
Mit den bisherigen Ergebnissen kamen letzendlich nur Knick- oder Z-Förderbänder in Frage. Jedoch scheint die Auswahl in diesem Bereich gerade beim Wunsch nach kompakter Bauweise und hoher Steigung sehr begrenzt zu sein. | |||
Da einige Hersteller ihre Produkte jedoch auf Maß anfertigen und auf ihren Webseiten entsprechend nicht alle möglichen Produkte präsentieren, wurden dennoch mit den in Abb. 31 gezeigten Abmessungen einige konkrete Anfragen gestellt. Aufgrund des Zeitmangels konnten die Anfragen jedoch nicht mit dem nötigen Nachdruck verfolgt werden, weshalb die Umsetzung der Rückführung zu Ende des Semesters noch aussteht und für die nächste Gruppe einen Hauptangriffspunkt darstellen sollte. | |||
=== Status der Anfragen === | |||
Der Status der Anfragen bei den verschiedenen Herstellern zum Ende des Semesters ist im Folgenden Aufgelistet: | |||
{| class="wikitable" | |||
|- | |||
! Hersteller: | |||
! Dorner/Geppert | |||
! Transtec | |||
! IVN | |||
! elcom | |||
|- | |||
! Status: | |||
| Mit benötigter Steigung nicht möglich | |||
| Keine konkrete Produktauskunft | |||
| Anfrage von Würth bezüglich kleinster Teilegröße | |||
| Postleitzahl für Vertriebspartnerzuweisung angefragt | |||
|- | |||
!Umsetzbarkeit: | |||
| Nein | |||
| Keine Auskunft | |||
| Keine Auskunft | |||
| Keine Auskunft | |||
|- | |||
!Preis: | |||
| Keine Auskunft | |||
| Keine Auskunft | |||
| Keine Auskunft | |||
| Keine Auskunft | |||
|} | |||
<ref name="Autor: Wolf"> Autor Jerome Wolf</ref> | |||
= Fazit = | |||
Folgende Punkte konnten zur Verbesserung der Separierung im WS18/19 realisiert werden: | |||
* Die Vorvereinzelung konnte durch Modifikation des Steigförderbandes erheblich verbessert werden. | |||
* Durch Integration der Vibrationsförderrinne werden die Teile weitgehend nacheinander und zentral auf das nachfolgende Förderband gebracht. | |||
* Durch gezieltes Ausschleusen unzureichend vereinzelter Teile in der neuen Separierungsbox wurde die Dauer des Separierungsprozesses erheblich verringert. | |||
* Die dadurch entstandene neue Separierung in 95% aller Fälle erfolgreich. | |||
<ref name="Autor: Bartnick"> Autor Madlen Bartnick</ref> | |||
=Ausblick= | |||
Folgende Aufgaben können von nachfolgenden Gruppen im Bereich der Separierung bearbeitet werden: | |||
* Realisierung einer automatischen Rückführung der nicht erkannten oder durch die Separierungsbox ausgeschleusten Teile. | |||
<br /> | <br /> | ||
<ref name="Autor: Bartnick"> Autor Madlen Bartnick</ref> | |||
= Autoren = | |||
<references /> | |||
''Dies ist ein Unterartikel von der [http://193.175.248.52/wiki/index.php/Legoteil_Z%C3%A4hlmaschine Legoteil_Zählmaschine], welcher den genauen Aufbau der Separierung beschreibt.'' |
Aktuelle Version vom 14. Februar 2019, 12:38 Uhr
Teammitglieder: Madlen Bartnick, Jerome Wolf,
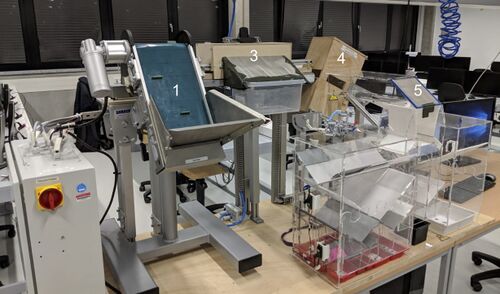
Dies ist ein Unterartikel von der Legoteil_Zählmaschine, welcher den genauen Aufbau der Separierung beschreibt.
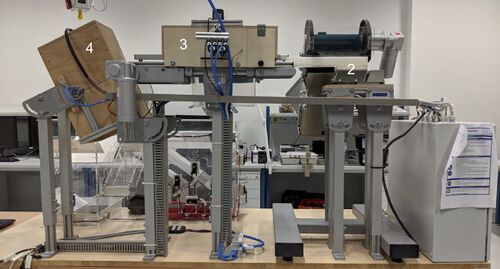
Die Separierung ist die erste Teilaufgabe der Legosortiermaschine. Sie sorgt dafür, dass die Legoteile einzeln und zentriert in die Bildverarbeitungsbox fallen, da dort nur einzelne Teile erkannt werden können.
Der aktuelle Aufbau der Separierung besteht aus einem Steigförderband mit Bunker (Abb. 1 Pos. 1). Dort werden die zu sortierenden Legoteile dem System zugeführt. Das Steigförderband transportiert eine Teilmenge der zugeführten Legoteile in eine darunterlegende Vibrationsförderrinne (Abb. 2 Pos. 2), in der diese dann zentriert und weiter vereinzelt werden. Durch die Vibration gelangen die Teile auf ein weiteres Förderband, welches diese durch eine Separierungsbox (Position 3) transportiert.
Die in der Separierungsbox integrierte Kamera liefert Momentaufnahmen der auf dem Transportband beförderten Teile. Mittels Bildverarbeitung wird die Anzahl der auf dem Band liegenden Teile in einem festgelegten Bereich ermittelt. Falls sich mehrere Teile in diesem Bereich befinden, werden mit Hilfe von Druckluftdüsen gezielt einzelne Teile in einen Auffangbehälter befördert. Nach der Separierungsbox befinden sich die Teile einzeln und zentriert auf dem Förderband und fallen von dort aus zur Erkennung in die Bildverarbeitungsbox (Abb. 1 Pos. 4).
Durch diesen Aufbau wurde das im Sommersemester 18 entwickelte Konzept zur Verbesserung der Separierung umgesetzt.
Ansatzpunkte des Konzepts:
- Modifikation des Steigförderbands zur besseren Vereinzelung der Teile
- Integration einer Vibrationsförderrinne zur Zentrierung der Teile
- Umbau der Separierungsbox zur Aussortierung nicht vereinzelter Teile
Die Umsetzung des Konzepts im Wintersemester 18/19 soll Inhalt dieses Artikels sein.
[1]
Modifikation des Steigförderbands zur besseren Vereinzelung der Teile
Da das Steigförderband im Ausgangszustand viel zu viele Teile auf einmal befördert hat (vgl. Abb. 5), wurde dieses modifiziert. Dazu wurden im vorherigen Semester ein neuer Fördergurt und Stollenmaterial bestellt, welche in diesem Semester dann durch Klebeverbindungen zu einem individuellen Stollengurt zusammengefügt wurden. Dabei wurden die Stollen zunächst provisorisch befestigt und verschiedene Anordnungen getestet. Nach und nach wurden die Stollen entfernt und verkleinert, bis sich das optimale Layout für die Vereinzelung ergeben hat (vgl. Abb. 6). In diesem Layout sind nun über den gesamten Gurtumfang verteilt sechs Stollen angebracht, die gemeinsam die gesamte Breite des Gurtes einmal abdecken. Damit die Teile neben den kleinen Stollen nicht aus dem Bunker fallen, musste der Abstreifer angepasst werden. Dazu wurde dieser in schmale Streifen geschnitten, sodass er sich automatisch an die Größe der Stollen anpassen kann. Um die Gesamtstabilität zu erhalten, wurde ein Blech angefertigt und zusammen mit dem Abstreifer oberhalb der Stollen eingebaut (vgl. Abb. 7). Das Ergebnis der Modifikation ist nun eine wesentlich geringere Menge an Teilen, die gleichzeitig durch das Steigförderband gefördert werden (vgl. Abb. 8).
-
Abb. 5: Steigförderband vor der Modifikation
-
Abb. 6: Neues Layout der Stollen
-
Abb. 7: Abstreifer zwischen Bunker und Stollen
-
Abb. 8: Steigförderband nach der Modifikation
Integration einer Vibrationsförderrinne zur Zentrierung der Teile
Um die Teile, die von dem Steigförderband aus dem Bunker befördert werden weiter zu vereinzeln und zusätzlich zu zentrieren, wurde eine Vibrationsförderrinne in den Prozess integriert. Zuvor sind die Teile vom Steigförderband aus dem Bunker direkt auf das Förderband gefallen, welches durch die Separierungsbox zur Bildverarbeitungsbox führt. Dabei wurden die Teile nicht gleichmäßig sondern haufenweise auf dem Förderband verteilt. Diese Haufen führen im weiteren Prozess zu Problemen, da die Bildverarbeitung nur einzelne Teile erkennen kann. Durch die Integration der Vibrationsförderrinne wurde die Haufenbildung auf dem Förderband erheblich gesenkt, da diese die Teile weitgehend hintereinander und zentriert auf das Förderband legt.
Die zur Integration durchgeführten Arbeitsschritte werden nachfolgend genauer erläutert.
Montage des Vibrationsantriebs in der Anlage
Um die Vibrationsförderrinne in den Prozess integrieren zu können, musste im ersten Schritt das Förderband, welches durch die Separierungsbox führt, durch ein kürzeres Förderband ersetzt werden. Danach wurde eine Grundplatte aus Aluminiumprofil und Holz erstellt (vgl. Abb. 9). Auf diese Grundplatte wurde im nächsten Schritt der Vibrationsantrieb montiert (vgl. Abb. 10). Zum Schluss wurde die Grundplatte mit Vibrationsantrieb durch zwei höhenverstellbare Ständer unterhalb des Bunkerbandes montiert (vgl. Abb. 11).
-
Abb. 9: Aufbau der Grundplatte
-
Abb. 10: Vibrationsantrieb montiert auf der Grundplatte
-
Abb. 11: Montage innerhalb der Anlage
Elektrischer Anschluss und Ansteuerung des Vibrationsantriebs
Nachdem der Vibrationsantrieb mechanisch integriert wurde, musste dieser elektrisch eingebunden werden. Dazu wurde er zunächst wie in vorherigen Semester geplant angeschlossen. Der erste Test zeigte jedoch, dass die Vibrationsleistung sowie die dadurch verursacht Lautstärke viel zu groß war. Daraufhin wurde durch einen Versuch die optimale Spannung zur Ansteuerung des Vibrationsantriebs ermittelt und ein Widerstand vorgeschaltet (vgl. Abb. 12). Dadurch wurden Leistung und Geräuschentwicklung optimiert und die Vibrationsförderrinne konnte auch programmtechnisch ins System integriert werden. Dazu wird diese gemeinsam mit dem Förderband, welches durch die Separierungsbox führt, gestartet und gestoppt (vgl. Abb. 13).
-
Abb. 12: Verdrahtungsschema des Vibrationsantriebs
-
Abb. 13: Ansteuerung des Vibrationsantriebs über den Arduino
Konstruktion der Förderrinne
Nach der Integration des Vibrationsantriebs in den Prozess folgte die Konstruktion der Förderrinne, in der die Teile später von dem Abwurf des Bunkerbands bis zum nachfolgenden Förderband transportiert werden. Dazu wurde im vorherigen Semester eine Rinne mit halbrundem Profil als beste Fördermöglichkeit ermittelt. Damit diese Förderrinne auf dem Vibrationsantrieb montiert werden kann, ohne dass die Schraubverbindungen im Inneren der Förderrinne liegen, wurde eine Montageplatte als Verbindungsglied konstruiert (vgl. Abb. 14). Diese Montageplatte soll auf den Vibrationsantrieb mittels Zylinderkopfschrauben befestigt werden. Die Förderrinne soll über eine trapezförmige Führungsschiene eingeschoben und mit einem Endstück mit vier Schrauben in der Führung fixiert werden. Die Förderrinne wurde so lang konstruiert, dass sie sich mit dem Förderband knapp überschneidet. Dadurch ist eine einwandfreie Übergabe gewährleistet. Das halbrunde Profil wurde so ausgelegt, dass auch das breiteste Legoteil problemlos gefördert werden kann. Die Unterseite der Förderrinne wurde mit dem Gegenstück der trapezförmigen Führungsschiene versehen (vgl. Abb. 15). So können die Einzelteile zusammen mit dem Vibrationsantrieb zum Gesamtsystem Vibrationsförderrinne zusammengesetzt werden (vgl. Abb. 16).
Die erstellten CAD-Dateien sind in SVN hinterlegt.
-
Abb. 14: Montageplatte zur Verbindung von Vibrationsantrieb und Förderrinne
-
Abb. 15: Förderrinne
-
Abb. 16: Gesamtansicht der Vibrationsförderrinne
Druck und Einbau der Förderrinne
Nach Abschluss der Konstruktion wurden die Teile mit Hilfe eines 3D-Druckers hergestellt (vgl. Abb. 17). Im Anschluss daran wurden diese Teile nachbearbeitet und auf dem Vibrationsantrieb montiert (vgl. Abb. 18). Nach der Optimierung des Zusammenspiels zwischen den Förderbändern und der Vibrationsförderrinne wurde der Übergang von dem Steigförderband zur Vibrationsförderrinne durch Zusammensetzen mehrerer durch 3D-Druck hergestellter Teile und einer Plexiglasscheibe so gestaltet, dass alle Teile sicher in die Förderrinne fallen (vgl. Abb.19).
-
Abb. 17: Druck der Förderrinne
-
Abb.18: Montage der Förderrinne
-
Abb. 19: Übergang zwischen Bunkerband und Vibrationsförderrinne
Überarbeitung der Separierungsbox
Da bei der ehemaligen Box zur finalen Vereinzelung die Teile auf dem Band zurückgeschoben wurden, würde dieses Vorgehen das komplette Konzept der Vereinzelung und Zentrierung durch das modifizierte Band und die Vibrationsförderrinne stören, da sich auf diese Weise erneut die unerwünschten Teilehaufen bilden würden. Durch die nach aktuellem Stand voraussichtlich sehr gut Vereinzelung vor der Bildverarbeitungsbox, wurde diese so umgebaut, dass Teile, welche zu nahe beisammen liegen, aus dem System befördert werden. Diese können im späteren Verlauf der Teilerückführung zugeführt werden und werden so erneut verarbeitet. Ein Stillstand durch die Bildung von Teilehaufen wie beim alten Konzept wird so vermieden.
Umbauarbeiten
Um das neue Konzept umzusetzen mussten zunächst einige Umbauarbeiten vorgenommen werden.
Umbau des Förderbandes
Um Platz für die Integration einer Vibrationsförderrinne zur Zentrierung der Teile zu schaffen, musste vor dem Umbau der Separierungsbox jedoch zunächst das darunter liegende Förderband verkürzt werden. Hierzu wurde das von vohrerigen Iterationen der Maschine übrig gebliebene Band verwendet, da dieses bereits die idealen Abmaße besaß. Somit wurde das alte Band demontierung und ohne großen Aufwand durch das alternative Band ersetzt. Zudem wurden Bandbegrenzung und Halterung für die Box modifiziert, um einen seitlichen Auswurf der Teile zu erlauben. Der Gesamte Bandaufbau vor der Montage der Separierungsbox ist in Abb. 20 zu sehen.
-
Abb. 20: Umgebautes Förderband mit Lücke für Teileauswurf
Konstruktion und Aufbau der neuen Bildverarbeitungsbox
Die neue Separierungsbox wurde zunächst in CAD Konstruiert, wie in Abb. 21 und Abb. 22 zu sehen. Das Design lehnt sich dabei an die alte Separierungsbox an, wobei entsprechende Änderungen wie seitliche Schlitze für die Düsen, sowie eine große Lücke für den Auswurf eingearbeitet wurden.
-
Abb. 21: CAD Modell Ansicht 1
-
Abb. 22: CAD Modell Ansicht 2
Anschließend wurde die Box aus Holz gefertigt. Dazu wurden zunächst die einzelnen Holzplatten zusammengeschraubt, sowie die entsprechenden Ausschnitte und Löcher hinzugefügt. Nach der Montage von LEDs (Abb. 24) und Düsen (Abb. 23) wurde die Box auf dem Förderband Montiert. Diese erste Version der neuen Box ist in Abb. 25 zu sehen.
-
Abb. 23: Anbringung der Druckluftdüsen
-
Abb. 24: LED-Konfiguration in der Box
-
Abb. 25: Erste Version der neuen Box
Im weiteren Verlauf wurden noch einige kleine Änderungen vorgenommen. So waren die Düsen in den alten Halterungen nicht frei Drehbar, was für eine sehr eingeschränkte Flexibilität bei Montage und Positionierung sorgte. Entsprechend wurden auch neue Düsenhalterungen in CAD konstruiert und 3D-gedruckt. Dadurch können die Düsen nun frei gedreht werden und sind in der Positionierung flexibler. Insbesondere konnten die Düsen somit näher zusammengebracht werden, wodurch der Separierungsalgorithmus die Teile besser aus dem System befördern kann.
-
Abb. 26: CAD Modell der neuen Düsenhalter
-
Abb. 27: Finale Version der neuen Box mit neuen Düsenhaltern und verbesserter Düsenposition
Separierungsalgorithmus

Nach den Umbauarbeiten an der Box wurde der entsprechende Steuerungsalgorithmus implementiert.
Farbfilter
Die Erkennung von einzelnen Teilen in der Separierungsbox ist mithilfe einer Farbmaske realisiert. Dabei wird die Farbe des Förderbandes, welches sich unter den Teilen befindet, aus dem Bild herausgerechnet. Übrig bleiben entsprechend die einzelnen Teile auf dem Band. Zwar können auf diese Weise nicht alle Teile zu 100% einzeln erkannt werden, jedoch stellen die auf diese Weise nicht identifizierbaren Teileanhäufungen eine eher seltene Ausnahme dar. Die Farbmaske kann dabei mit dem sogenannten Color Thresholder in MATLAB erstellt werden. Der entsprechende Prozess ist bereits in der Maskenbildung der Bildverarbeitung erklärt und kann dort entsprechend nachvollzogen werden. Das Ergebnis nach diversen Iterationen mit verschiedenen Masken und Kameraeinstellungen ist in Abb. 29 zu sehen.
-
Abb. 29: Farbmaske der Separierung
-
Abb. 30: Beispiel für Düsenansteuerung der Separierung
Programmablauf
Der Algorithmus der Separierung folgt anschließend im Grunde einem einfachen Ablauf:
- Die benötigten Parameter für serielle Kommunikation, Bildbearbeitung und Separierung werden festgelegt.
- Das Bild wird aufgenommen und der Farbfilter wird angewendet.
- Die resultierende Binärmaske wird zugeschnitten um unerwünschte Bildbereiche zu entferne, kleine Objekte (Artefakte) werden gelöscht und die Schwerpunkte aller übrigen Objekte werden berechnet.
- Sind die Schwerpunkte der Objekte in X-Richtung zu nahe beieinander und befindet sich das hintere Teil vor einer Düse, so wird dieses aus dem System befördert.
- Zur Visualisierung werden das Originalbild und die Binärmaske mit Schwerpunkten, sowie die Düsen mit aktuellem Ventilzustand (blau = geschlossen, rot = geöffnet) in der GUI angezeigt.
Der genaue Ablauf ist zudem nochmals graphisch in Abb. 28 dargestellt. In Abb. 30 ist hingegen eine beispielhafte Visualisierung der Ansteuerung zu sehen. Nach der Anwendung der Farbmaske und dem Zuschneiden des Bildes sind die einzelnen Teile in Weiß zu erkennen. Die Schwerpunkte der Teile werden durch einen kleinen roten Kreis dargestellt. Da sich im Konkreten Beispiel das Teil auf der linken Seite zu nahe am vorherigen Teil befindet und dieses sich zudem vor einer der beiden Düsen befindet, wird die Düse aktiviert und würde das Teil somit aus der Box befördern.
Teilerückführung
Die Teilerückführung soll dazu dienen, dem Bunker nicht erkannte sowie ausgeworfene Teile erneut zuzuführen. Dabei wurden verschiedene Optionen in Erwägung gezogen, welche im Folgenden genauer erläutert werden sollen.
Bewertung der Rückführungsoptionen
Prinzipielle Bewertung
Zunächst wurden für die Rückführung folgende grundsätzlichen Rückführungsmöglichkeiten in Erwägung gezogen:
Förderband | Schneckenförderer | Druckluftförderung | Teilerutsche | |
---|---|---|---|---|
Vorteile |
|
|
|
|
Nachteile |
|
|
|
|
Umsetzbarkeit | Theoretisch machbar, Steigung ggf. problematisch | Zerquetschte Teile nicht akzeptabel | Nicht zuverlässig genug | Durch Höhenunterschied nicht machbar |
Typen von Steigförderbändern
Da die einfacheren oder experimentellen Methoden bei der Rückführung kein gutes Ergebnis versprachen, fiel die Auswahl letztendlich auf das erprobte Förderband zur Rückführung. Jedoch gibt es auch hier verschiedene Arten die in Frage kämen:
Steigförderband | Knickförderband | Z-Förderband | |
---|---|---|---|
Vorteile |
|
|
|
Nachteile |
|
|
|
Umsetzbarkeit | Nicht möglich da Teileaufnahme an Separierung nicht möglich | Möglich, aber Teileabwurf ungünstig | Ideal, aber Platz- und Steigungstechnisch schwierig |
Anfragen bei Herstellern
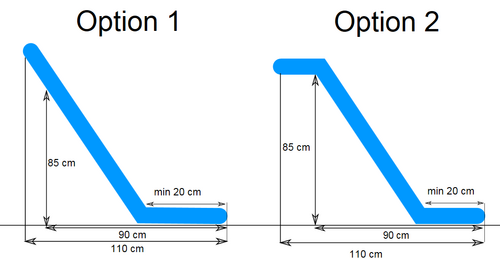
Mit den bisherigen Ergebnissen kamen letzendlich nur Knick- oder Z-Förderbänder in Frage. Jedoch scheint die Auswahl in diesem Bereich gerade beim Wunsch nach kompakter Bauweise und hoher Steigung sehr begrenzt zu sein. Da einige Hersteller ihre Produkte jedoch auf Maß anfertigen und auf ihren Webseiten entsprechend nicht alle möglichen Produkte präsentieren, wurden dennoch mit den in Abb. 31 gezeigten Abmessungen einige konkrete Anfragen gestellt. Aufgrund des Zeitmangels konnten die Anfragen jedoch nicht mit dem nötigen Nachdruck verfolgt werden, weshalb die Umsetzung der Rückführung zu Ende des Semesters noch aussteht und für die nächste Gruppe einen Hauptangriffspunkt darstellen sollte.
Status der Anfragen
Der Status der Anfragen bei den verschiedenen Herstellern zum Ende des Semesters ist im Folgenden Aufgelistet:
Hersteller: | Dorner/Geppert | Transtec | IVN | elcom |
---|---|---|---|---|
Status: | Mit benötigter Steigung nicht möglich | Keine konkrete Produktauskunft | Anfrage von Würth bezüglich kleinster Teilegröße | Postleitzahl für Vertriebspartnerzuweisung angefragt |
Umsetzbarkeit: | Nein | Keine Auskunft | Keine Auskunft | Keine Auskunft |
Preis: | Keine Auskunft | Keine Auskunft | Keine Auskunft | Keine Auskunft |
Fazit
Folgende Punkte konnten zur Verbesserung der Separierung im WS18/19 realisiert werden:
- Die Vorvereinzelung konnte durch Modifikation des Steigförderbandes erheblich verbessert werden.
- Durch Integration der Vibrationsförderrinne werden die Teile weitgehend nacheinander und zentral auf das nachfolgende Förderband gebracht.
- Durch gezieltes Ausschleusen unzureichend vereinzelter Teile in der neuen Separierungsbox wurde die Dauer des Separierungsprozesses erheblich verringert.
- Die dadurch entstandene neue Separierung in 95% aller Fälle erfolgreich.
Ausblick
Folgende Aufgaben können von nachfolgenden Gruppen im Bereich der Separierung bearbeitet werden:
- Realisierung einer automatischen Rückführung der nicht erkannten oder durch die Separierungsbox ausgeschleusten Teile.
Autoren
Dies ist ein Unterartikel von der Legoteil_Zählmaschine, welcher den genauen Aufbau der Separierung beschreibt.